Precision die casting is a process of direct-metal injection molding. Mold is made to be smooth and fine, so that the surface finish looks just like an injection molded plastic part . Precision die castings have high dimensional accuracy, good surface quality, good mechanical properties, long shot weight capability, & thin wall section capabilities. The dimensional tolerances are ±0.002 inches (±0.05mm) or better on straight walls +/- 0 .005 inches (0.13mm) or better on tapered areas for aluminum alloys 1 inch (25mm) per 12 inches for steel alloy 5 inch (125mm) per foot long
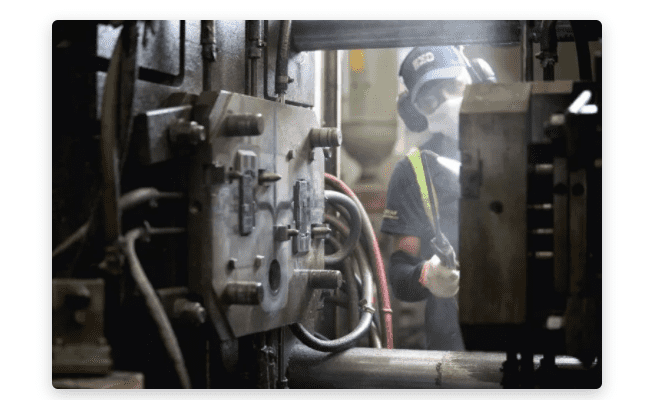
These figures are intended as a rough guide only.
The main purpose of precision die casting is to recover metal. Up to 50% of the metal is recycled. Some processes allow 90% recovery. For example, Volkswagen manufactures 5,000 engine blocks per day; 4,500 are collected and reused as new engine blocks. Only 500 become scrap because the holes wear out. This process allows for large quantity production at low cost without significant waste .
The typical precision die casting machine consists of a frame, a table that holds a mold/die set with runner system attached, a hydraulics unit (for shot delivery), an operator’s platform for the operator to see into the machine and monitor operations, and some storage space on board or nearby where work in progress can be stored until completed .
There are three main types of dies: conventional hot-chamber, cold-chamber, and direct. Conventional hot-chamber die casting is the original die casting technology. The machine is equipped with a piston cylinder arrangement to inject molten metal under pressure into an ejection chamber cooled by air or water to solidify the shot (or slug) within it . After ejecting this shot, the mold closes automatically and gets back to position for subsequent shots .
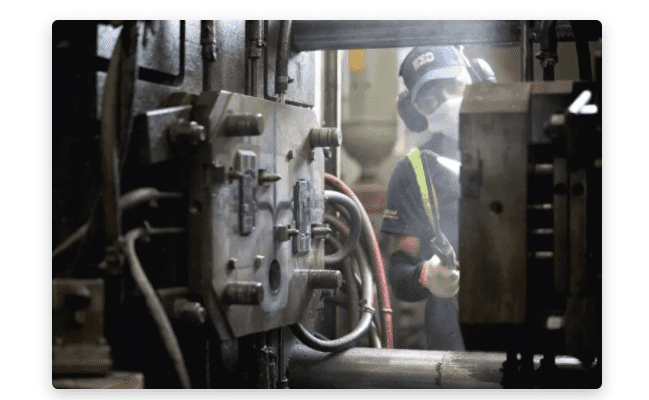
Cold chambers are commonly used when parts made of aluminum alloy need to be heat treated after casting. The cold chamber machine has a die-closing mechanism that doesn’t require the use of heated dies, as found in the hot-chamber machines. This is why it’s called a “cold chamber”. The injection takes place in a cold chamber inserted in the mold .
Direct die casting is a relatively new technology that overcomes some of the limitations of conventional die casting and cold chamber die casting processes. In direct die casting, the molten metal is injected into the mold through a direct path from the injector . For this reason, it’s also called “direct/hot-chamber die casting”. The advantage of direct die casting is that the end product has a better surface finish since there aren’t any ejection issues.
Post processing:
Materials used in precision die castings are aluminum and magnesium alloy. These materials have good mechanical properties and good corrosion resistance when compared to other metals such as steel. This means they can be easily machined after casting to remove burrs from inside the part or from the surface. The parts can also be heat treated if required to improve the strength and hardness of the metal.
The main disadvantage of die casting is that it is a relatively expensive process compared to other metal manufacturing processes such as machining or forging. However, the high degree of precision and good surface finish make it a popular choice for many products where appearance is important.