10 Ways to Save Costs When Manufacturing Your Products
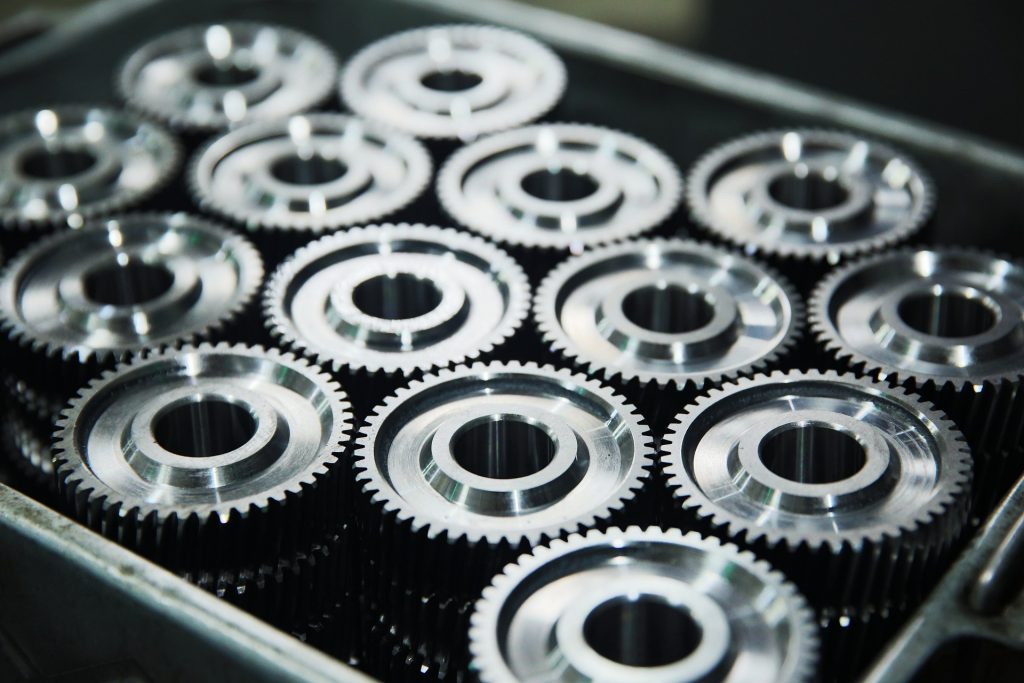
In a world that has been increasingly dematerializing and turning towards more e-commerce, it is common knowledge that the price of any given product is a key factor in its success.
To be competitive means being able to manufacture your products at the lowest cost possible. Keeping this in mind, here are 10 ways manufacturing companies can reduce costs without sacrificing quality.
1. Explore Manufacturing Options
One easy way to reduce the cost of manufacturing is to explore options for doing it yourself, rather than hiring an external supplier. Depending on your business location, you may be able to find a facility within walking distance that specializes in producing specialty components. Also, taking advantage of 3D printing services can enable you to prototype and produce small-batch items without investing in expensive equipment. A new technology called CNC waterjet cutting can also provide a low-cost solution for cutting and engraving larger components like circuit boards and glass panels, enabling some entrepreneurs to start with just an idea and do everything themselves from design through manufacture.
2. Get Creative with Layouts
The layout of your manufacturing space has a big impact on how efficiently your employees can work. If they’re doing a lot of unnecessary walking or if their productive time is being cut short due to inefficient traffic patterns, you might be able to increase their productivity and save money by rearranging items within the space.
3. Minimize Inventory and Transportation Costs
When possible, use materials that enable you to minimize inventory and transportation costs: sheet metal, threaded rod, bearing assemblies and fasteners are just a few examples for which special packaging methods exist that enable parts to be shipped in compact 99 percent efficient configurations. Also, consider using raw material suppliers who offer to ship combined with material purchases as another way to reduce warehouse storage requirements. Then finally you can monitor your inventory regardless of where it is stored with MRP software.
4. Simplify design
Small changes made early on in the design process can greatly impact costs. Every time you add weight or size to a part, it requires extra material, and the cost of your final product will increase accordingly. For instance, one redesign might allow you to replace four different parts with a single part that performs all the same functions while using less material.
5. Reduce Non-Value-Added Processes
Many manufacturing processes — such as manual welding and soldering — involve activities that don’t add value to the finished product but add an expense in the components purchased and labor used. Try to replace these types of non-value-added processes with automated alternatives whenever possible, such as purchasing pre-made circuit boards rather than manually building them yourself and purchasing precisely calibrated equipment instead of performing standard maintenance activities yourself.
6. Ignore Trends That Don’t Add value
When your company is starting out, you might be tempted to keep up with industry trends in product design and functionality, but this can often drive costs up without adding significant value for customers. Instead, take a hard look at the market and ask what your target audience actually needs types of features, then focus on other items that provide the best return on investment when it comes time to invest in production equipment.
7. Take Advantage of Automation Opportunities
Automation opportunities can come in any size — from small assembly line robots to fully automated CNC machines that integrate directly into existing manufacturing ERP software — so don’t overlook these high-efficiency alternatives just because they’re not currently in your facility.For instance, automated equipment like Australia dust extraction systems might be able to reduce or eliminate the need for certain types of human labor, freeing up employees to perform higher-value activities — leading to increased productivity and lower costs at the same time. Dust extraction systems automatically remove dust or other waste products of the manufacturing process, manually removing this waste would be timely and requires little to no skill.
8. Consider Outsourcing
Outsourcing can provide a low-cost way for manufacturers with limited resources to successfully bring new products into the market quickly without investing in expensive production equipment or hiring additional staff members that they don’t have the budget for just yet. However, you need to carefully choose your supplier partners so that you’re maximizing value rather than taking on unnecessary risk by relying on unreliable suppliers overseas who don’t understand your cultural norms and business goals.
9. Use Packaging That Adds Value
Modern packaging can add significant value to finished products in various ways. One common example is using shipping boxes that double as point-of-sale promotional displays when filled with the product, such as putting books into book covers, placing bottles inside cardboard carrying cases, and folding compact mirrors around makeup compacts.
10. Minimize Transportation Costs
Somebody must pay transportation costs, so whether it’s customers or suppliers who are covering these expenses — or you’re doing it yourself within your own facility — look for ways to use fewer trucks and/or ships to keep these costs down:
- adjust shipment sizes whenever possible
- build smaller units that require less space during shipments
- reduce the weight of each shipment wherever possible
- consolidate the number of shipments that go out per day, and transport goods inside buildings whenever possible rather than outside