What are the 5 common types of CNC machines?
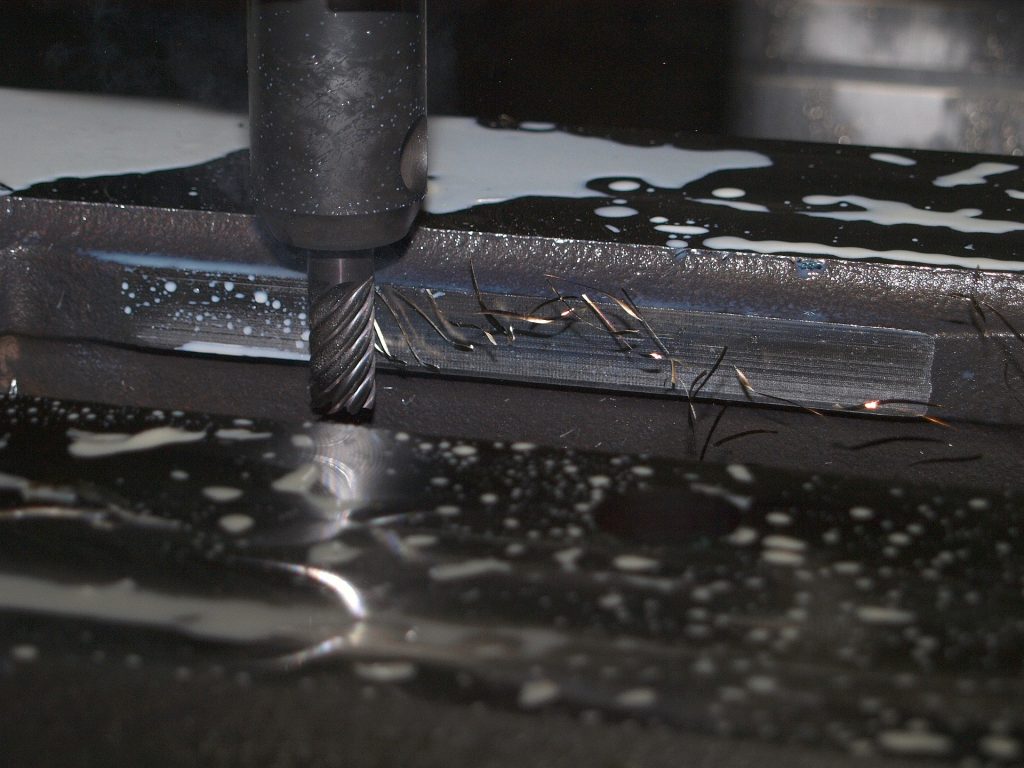
A CNC machine is a computer-controlled tool that performs various tasks. CNC machines are used in a wide variety of commercial and industrial settings.
CNC stands for Computer Numerical Control. These machines can move precisely on three axes (XYZ) by using computer software. The different CNC machines each use different drives for movement along the three axes. Each machine has its own unique abilities and can complete certain jobs that other machine types cannot do quite as effectively.
When most people think of CNC machines, they envision a lathe or a milling machine. However, there are many CNC machining techniques. In fact, there are five very common types of CNC machines: the lathe, the milling machine, router machines, laser cutters, and plasma cutters.
Lathe CNC
Lathe CNC machines are designed to spin materials at high speeds. Lathes are used in the casting, shaping, boring, scraping, and sanding of various materials.
Lathes are able to create large parts that would otherwise be impossible or impractical to craft manually. These machines vary in size and function depending on their intended use. Some commercial lathes can be as large as ten feet in length.
The Milling Machine
Milling machines carve using a rotating milling bit. A wide array of materials can be carved, including metals, aluminum, wood, plastics, and composites. Mainly used in metalworking, milling machines typically use a computer numerical control (CNC) system.
The milling machine is generally considered the second most common CNC machine after lathes.
The CNC Router
The CNC router is used to carve 3-dimensional forms from wood by driving an end mill bit through the material. This machine can be used to create door and window frames, moldings for hardwood floors, or even chair rail and crown molding for interior home design. Like the CNC mill, a CNC router is typically used in woodworking and metalworking.
Home routers can be modified to use as a CNC router by attaching them to a frame with wheels and connecting them to a computer and feed mechanism. The frame allows the router to move around when carving, while the computer controls the movement of the bit.
CNC Plasma Cutters
Plasma cutters produce high-quality cut designs in plastic, sheet metal, and light alloys. The CNC plasma cutter uses compressed air to shoot ionized gas (such as oxygen) through a small orifice at the material that is to be cut.
A current applied across two tungsten electrodes rips the electrons away from some of the gas molecules, which are then ionized. This makes the gas into plasma, at a temperature of around 16000 degrees Celsius. Finally, high velocity oxygen ions are ejected from the nozzle, cutting through the material being worked on.
CNC Laser Cutter
Laser cutters can be used to cut soft metals such as aluminum, wood, and leather. Larger machines are also capable of cutting through harder materials such as acrylic glass and carbon fiber composites.
The laser beam is usually produced by a high-power gas laser which uses gases such as fluorine, oxygen or carbon dioxide.
Benefits of CNC Machining
CNC machining offers a range of benefits over conventional manual methods:
Easy Setup – When you want to make a different part or perform a quick modification, CNC machining is made easy with the use of a computer. Most machines can be controlled using CAD/CAM software, which allows you to design your part’s geometry on your computer or laptop. You can also directly import or export data between CAD programs so that no file conversions are necessary during the process.
Part Accuracy – The CNC machine controls the movement of its tool to within +/-0.001 inches, guaranteeing that your part will be made to precise dimensions.
Speed – Unlike manual machining, CNC machines can complete projects in a fraction of the time.
Parts can be produced on demand rather than having to wait for material delivery, which means less time from design to the final part.
Resource Savings – Most CNC machines are automated, needing only a single operator. Manual processes often require several people just for loading and unloading materials alone. In addition, the need for raw material is reduced because you don’t have reshaping losses due to breakage or other factors.
Lower Labor Costs – A typical CNC machine only needs a single operator to complete its tasks, as opposed to several people for manual machining.
Higher Quality – With improved accuracy comes higher quality. Parts made on a CNC machine will be more precise and reduce the need for hand-finishing or rework after an automatic process has taken place. And there you have it! You now know the 5 common types of CNC machines. Thank you for reading.