The Advantages of Electric Rotary Actuators in Automotive Applications
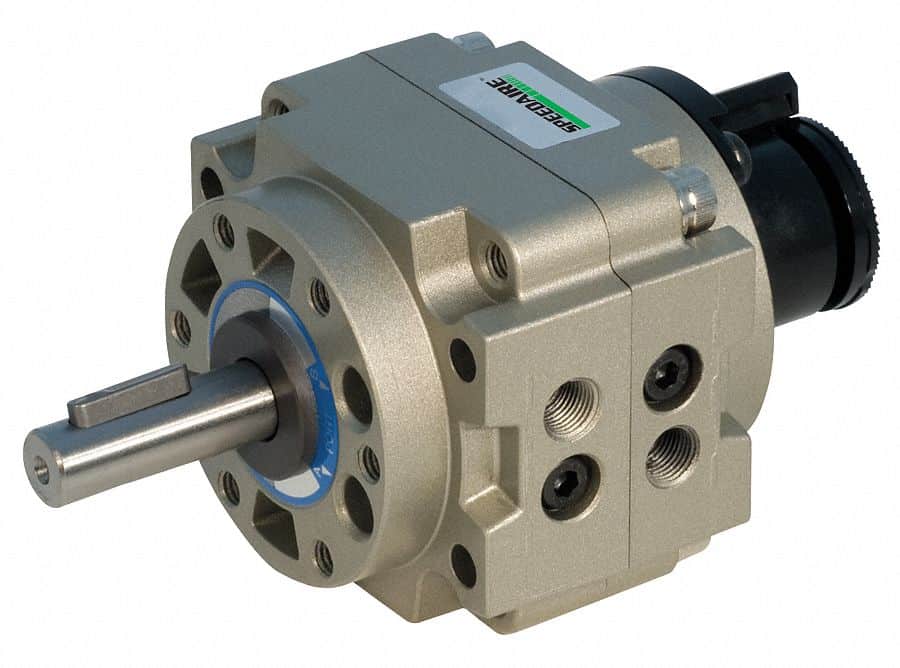
Electric rotary actuators are a type of electromechanical actuator used to automate and control the movement of mechanical components in automotive applications. They are well-suited for applications that require precise, repeatable, and reliable motion control.
They are becoming increasingly popular in automotive applications due to their high efficiency, cost-effectiveness, and ease of integration. This article will discuss five advantages of an electric rotary actuator in automotive applications.
1. Accuracy in Controlling And Positioning
One of the primary advantages of electric rotary actuators in automotive applications is their accuracy in controlling and positioning. It is equipped with sophisticated control systems that allow for precise movement of the mechanical components. This is especially important for applications such as engine management and transmission control, where the accuracy of the actuator is essential for proper operation.
Furthermore, it can be programmed to adjust the position of the mechanical components in increments as small as a few microns, allowing for accurate and precise control of the components. This allows the actuator to be used in applications such as fuel injection systems and exhaust valves where the accuracy of the actuator is critical for proper operation. Additionally, it can control the position of the camshafts in the engine management system, allowing for precise control of the engine’s timing.
2. Easy Integration
Electric rotary actuators are designed to be easily integrated into existing systems, making them ideal for automotive applications. They are available in various sizes and mounting configurations, allowing them to fit into tight spaces and provide precise control of the mechanical components. Additionally, they are designed to be easily connected to existing systems, allowing them to be quickly and easily integrated into the system. It eliminates the need for extensive rewiring, which can be time-consuming and costly.
Moreover, it can be connected to various control systems, such as sensors and limit switches, allowing easy integration into the existing system. This enables the actuator to be used in applications such as transmission control and braking system control, where integration with existing systems is critical for proper operation.
3. Minimal Maintenance
Electric rotary actuators require minimal maintenance, which makes them ideal for automotive applications. They are designed to operate in harsh environments, and their components can withstand large temperature changes and vibration levels. This makes them more reliable and less prone to failure.
It is also designed to be self-lubricating, so they require little to no grease, reducing maintenance costs. Electric rotary actuators are also designed with built-in diagnostic features, allowing quick and easy troubleshooting and maintenance. This makes them an ideal choice for automotive applications that require minimal downtime.
4. High Precision Level
A high-precision electric rotary actuator level also allows for faster response times and improved dynamic stability in automotive applications. This can help reduce vibration and noise, increasing a vehicle’s overall comfort and safety. It can also provide higher torque and speed ranges than other actuators, allowing for more efficient and powerful operation.
Electric rotary actuators also provide a wide range of control options, allowing for easy and flexible integration into various automotive systems. This makes it possible to customize the control of different components, allowing for more precise and efficient operation. Furthermore, the high precision level of the electric rotary actuators ensures that the components are moved in the desired way, leading to better-performing vehicles.
5. No External Sensor
Electric rotary actuators do not require an external sensor to operate, which helps reduce the system’s cost and complexity. This is because the actuator is self-contained and does not require additional sensors. This eliminates the need for additional wiring, which can be expensive and time-consuming. Furthermore, the lack of external sensors also allows for improved reliability and longer operating life, as there are fewer components to maintain.
The Bottom Line
The absence of external sensors also helps reduce the system’s complexity, as the system can be operated with minimal input and oversight. This makes it an ideal choice for applications with limited space or user interaction is not desired. The lack of external sensors also increases safety as there is no need to worry about potential hazards caused by external sensors.