Transforming Material Handling with Custom Conveyor Packages
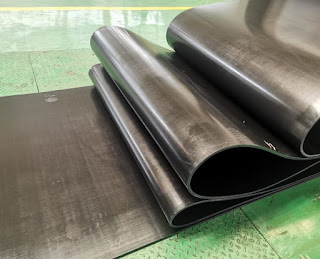
Custom conveyor packages are revolutionizing material handling by offering tailored design and engineering solutions that cater to specific site requirements. These systems incorporate modular components, advanced materials, and custom belt configurations to ensure optimal performance and flexibility. These custom packages enhance operational efficiency and longevity by seamlessly integrating with existing systems and incorporating specialized applications like dust suppression and heat-resistant belts. Key components such as variable speed drives, gravity take-up units, and impact beds are included to optimize functionality and reduce maintenance needs. Accessories are crucial in maintaining seamless operation, extending equipment lifespan, and enhancing safety. Additionally, using a mining conveyor belt specifically designed for harsh mining environments ensures robust performance and durability in demanding conditions.
Custom Conveyor Packages
Detailed Customization Options for Conveyor Systems
- Tailored Design and Engineering:
- Site-Specific Design: Custom conveyor packages start with an in-depth analysis of the mining site. Engineers assess the unique challenges and requirements of the location, including terrain, material types, load capacities, and operational goals. This information is used to design a conveyor system perfectly suited to the specific environment.
- Modular Components: The design incorporates modular components that can be easily adjusted or expanded as operational needs change. This flexibility ensures that the conveyor system can adapt to future demands without requiring a complete overhaul.
- Advanced Materials Selection: Depending on the mining conditions, materials such as steel cords, Kevlar®, or specialized polymers may be chosen to enhance durability, reduce maintenance, and improve overall performance. For instance, a nylon conveyor belt might be selected for its exceptional strength and flexibility in specific applications.
- Custom Belt Widths and Lengths: Conveyor belts can be customized to various widths and lengths to accommodate the volume and type of materials transported. This ensures optimal material flow and minimizes the risk of spillage or bottlenecks.
- Incline and Decline Adjustments: Custom conveyors can be designed to handle specific inclines and declines, ensuring efficient material transport across different elevations within the mining site.
- Integration with Existing Systems:
- Seamless Integration: Custom conveyor systems are designed to integrate seamlessly with existing mining infrastructure, such as crushers, screens, and loading stations. This integration ensures a continuous and efficient flow of materials throughout the operation.
- Control Systems: Advanced control systems can be included to automate and optimize conveyor operations. These systems monitor belt speed, load weight, and operational conditions, allowing for real-time adjustments and minimizing downtime.
- Specialized Applications:
- Dust Suppression Systems: For sites where dust control is crucial, custom conveyors can be equipped with dust suppression systems to minimize airborne particles, improving air quality and reducing health risks for workers.
- Heat-Resistant Belts: Heat-resistant conveyor belts can be incorporated in environments with high temperatures to maintain performance and longevity.
- High-Impact Areas: For areas where materials are loaded onto the conveyor belt from significant heights or are particularly abrasive, reinforced belts and impact beds can be installed to absorb the shock and reduce wear.
Components Included in Custom Packages
- Conveyor Drives:
- Variable Speed Drives (VSDs): VSDs allow precise conveyor speed control, optimize energy use, and ensure smooth material flow. This is particularly useful in operations where material throughput needs to be adjusted based on varying conditions.
- High-Torque Drives: For applications requiring the transport of heavy loads, high-torque drives provide the necessary power to maintain consistent performance.
- Take-Up Units:
- Gravity Take-Up Units: These units automatically maintain proper belt tension, compensating for belt stretch and ensuring smooth operation.
- Fixed Take-Up Units: In applications where minimal belt stretch is expected, fixed take-up units provide a cost-effective solution for maintaining belt tension.
- Tail Sections:
- Standard Tail Sections: Designed for typical load conditions, these sections are built to handle regular material flow efficiently.
- Heavy-Duty Tail Sections: Heavy-duty tail sections are reinforced for high-impact or high-load areas to withstand extreme conditions and prevent damage to the conveyor system.
- Belt Starters:
- Soft Starters: These devices gradually ramp up the conveyor belt speed, reducing the mechanical stress on the system and extending the lifespan of the components.
- Direct Online Starters: Suitable for simpler systems, these starters provide a straightforward, cost-effective method for starting conveyor belts.
- Discharge Booms:
- Fixed Discharge Booms: Ideal for operations with a consistent discharge point, these booms ensure precise material placement.
- Telescopic Discharge Booms: These adjustable booms can extend or retract to reach different discharge points, providing flexibility in material handling.
- Conveyor Belts:
- General Purpose Belts: Designed for standard material handling applications, offering a balance of durability and flexibility.
- Specialty Belts: Includes heat-resistant, oil-resistant, and flame-retardant belts tailored for specific operational needs.
- Structure Components:
- Frames and Supports: Custom-designed frames and supports ensure the conveyor system is stable and securely anchored, even in challenging terrains.
- Idlers and Rollers: High-quality idlers and rollers reduce friction and wear, enhancing the conveyor belt’s efficiency and lifespan.
- Chutes and Guarding: Custom chutes direct materials efficiently onto the conveyor belt while guarding ensures worker safety by preventing accidental contact with moving parts.
Conveyor Accessories
Importance of Accessories for Seamless Operation
- Enhancing Efficiency and Performance:
- Operational Continuity: Conveyor accessories are crucial in maintaining conveyor systems’ continuous and efficient operation. Accessories minimize downtime and enhance productivity by ensuring that all components function harmoniously.
- Optimization of Material Flow: Properly selected accessories help optimize the flow of materials along the conveyor system. This optimization reduces bottlenecks and ensures smooth transportation, which is essential for maintaining high operational efficiency.
- Extending Equipment Lifespan:
- Protection Against Wear and Tear: Accessories such as impact beds, belt cleaners, and skirting systems protect the conveyor belt and other components from excessive wear and tear. This protection extends the equipment’s lifespan and reduces the frequency of maintenance and replacements.
- Minimizing Downtime: Accessories help minimize downtime caused by maintenance and repairs by preventing common issues like material spillage, belt misalignment, and buildup. This results in more consistent operation and lower overall maintenance costs.
- Enhancing Safety:
- Worker Protection: Safety accessories such as emergency stop switches, safety pull cords, and guarding systems are essential for protecting workers from potential hazards associated with conveyor systems. These accessories ensure that safety protocols are adhered to and that workers can operate in a safe environment.
- Compliance with Regulations: Proper use of safety accessories ensures compliance with industry safety standards and regulations. This compliance helps avoid legal issues and enhances the overall safety culture within the operation.
- Improving Material Handling:
- Material Control: Accessories like chutes, diverters, and feeders help control the flow and direction of materials on the conveyor system. This control ensures that materials are handled efficiently and accurately, reducing waste and improving overall productivity.
- Quality Control: Ensuring that materials are transported smoothly and without contamination or loss helps maintain the quality of the processed materials. This is particularly important in industries where material integrity is critical, such as food processing or pharmaceuticals.
Types of Accessories Available
- Belt Cleaners:
- Primary Belt Cleaners: Installed at the head pulley, primary belt cleaners remove the bulk of carryback material from the conveyor belt. They are essential for preventing material buildup and maintaining efficient belt operation.
- Secondary Belt Cleaners: Located further along the conveyor, secondary belt cleaners provide additional cleaning to remove any residual material left by the primary cleaner, ensuring a thorough cleaning of the belt.
- Impact Beds and Cradles:
- Impact Beds: Installed at loading zones, impact beds provide a cushion that absorbs the shock and impact of falling materials. This protection reduces belt damage and prevents material spillage.
- Impact Cradles: Similar to impact beds, cradles support the belt and provide a more uniform surface to absorb impact, further reducing wear and tear on the belt.
- Belt Tracking Systems:
- Tracking Idlers: These idlers help keep the conveyor belt aligned and centered on the conveyor structure, preventing misalignment and associated problems such as edge damage and spillage.
- Guiding Rollers: Placed at critical points along the conveyor, guiding rollers ensure that the belt stays on track, reducing maintenance and downtime caused by misalignment.
- Skirting and Sealing Systems:
- Skirt Boards: Installed along the sides of the conveyor belt at loading zones, skirt boards prevent material from spilling over the edges of the belt. They help contain the material and reduce cleanup efforts.
- Sealing Strips: These strips provide a tight seal between the skirting board and the conveyor belt, further preventing material spillage and dust generation.
- Chutes and Hoppers:
- Transfer Chutes: Designed to guide and control the flow of materials from one conveyor to another or from a conveyor to a storage bin, transfer chutes help minimize spillage and reduce wear on the conveyor belt.
- Loading Hoppers: These hoppers direct material onto the conveyor belt, ensuring a smooth and controlled transfer of materials, reducing spillage, and improving loading efficiency.
- Safety Accessories:
- Emergency Stop Switches: Placed at strategic points along the conveyor system, these switches allow workers to stop the conveyor in an emergency, enhancing safety quickly.
- Safety Pull Cords: These cords run along the length of the conveyor, enabling workers to stop the conveyor from any point along its path, providing an additional layer of safety.
- Guarding Systems: Protective barriers and guards prevent accidental contact with moving parts of the conveyor, reducing the risk of injuries.
- Dust Suppression Systems:
- Water Spray Systems: These systems spray a fine mist of water to suppress dust at transfer points and loading zones, improving air quality and reducing workers’ risk of respiratory issues.
- Fog Cannons: Fog cannons generate a mist that binds with dust particles, causing them to settle and reducing airborne dust in the surrounding area.
- Feeder Systems:
- Vibratory Feeders: These feeders use vibration to move materials onto the conveyor belt at a controlled rate, ensuring consistent material flow and preventing overloading.
- Apron Feeders: Designed for heavy-duty applications, apron feeders provide a robust solution for feeding large, heavy materials onto the conveyor system.
- Discharge Systems:
- Plows and Scrapers: These devices remove material from the conveyor belt at specific discharge points, ensuring precise and controlled unloading.
- Diverter Systems: Diverters direct materials to different discharge points, allowing for flexible and efficient distribution of materials.
Key Services and Products
Overview of Services
- Special Design and Fabrication:
- Custom Engineering Solutions: Custom Conveyor Solutions offers specialized design services tailored to each client’s unique requirements. This includes creating bespoke conveyor systems engineered to handle specific materials, load capacities, and operational conditions.
- Fabrication Excellence: Gram conveyor’s state-of-the-art fabrication facilities are equipped with advanced machinery and technology, enabling the production of high-quality conveyor components. The fabrication process includes precision cutting, welding, assembly, and finishing, ensuring that every component meets stringent quality standards.
- Prototyping and Testing: Custom Conveyor Solutions provides prototyping and testing services before full-scale production. This allows clients to evaluate the design and functionality of their custom conveyor systems, ensuring that all requirements are met and any necessary adjustments can be made prior to final production.
- Wireless Shaft Alignment:
- Precision Alignment Services: Gram conveyor offers wireless shaft alignment services to ensure the optimal alignment of conveyor shafts. Proper alignment is critical for reducing wear and tear, preventing mechanical failures, and extending the lifespan of the conveyor system. The wireless technology used allows for accurate and efficient alignment without the need for extensive downtime.
- Detailed Reporting: Clients receive comprehensive alignment reports that detail the condition of their equipment and provide recommendations for maintenance or adjustments. This proactive approach helps prevent costly breakdowns and ensures smooth operation.
- Steel Fabrication:
- Custom Steel Components: Gram Conveyor specializes in fabricating custom steel components for conveyor systems, including steel cord conveyor belts. These include frames, supports, chutes, and other structural elements critical for the system’s stability and durability.
- High-Quality Materials: The company uses high-grade steel to fabricate components that can withstand the harsh conditions of industrial environments, especially when used with a steel cord conveyor belt. Each component is designed for maximum strength and longevity, ensuring reliable performance.
- 3D Scanning Services:
- Advanced Measurement and Modeling: Custom Conveyor Solutions utilizes 3D scanning technology to create precise digital models of existing conveyor systems and components. This technology allows for accurate measurements and detailed analysis, facilitating the design of custom solutions that fit seamlessly into existing infrastructure.
- Reverse Engineering: 3D scanning is also used for reverse engineering, allowing the company to replicate and improve existing components. This service is particularly useful for replacing outdated or hard-to-find parts.
Range of Products
- Conveyor Belts:
- General Purpose Belts: These belts are designed for a wide range of material handling applications, offering a balance of durability and flexibility. They are suitable for transporting various materials, including aggregates, coal, and ore.
- Specialty Belts: Custom Conveyor Solutions offers a variety of specialty belts, including heat-resistant, oil-resistant, and flame-retardant belts. These belts are tailored for specific industrial applications, ensuring optimal performance in challenging environments.
- Nylon Conveyor Belts:
Known for their exceptional strength and flexibility, nylon conveyor belts are ideal for applications that require durable and reliable performance. These belts can handle heavy loads and are resistant to abrasion and impact.
- Conveyor Systems:
- Overland Surface Conveyor Systems: Designed to transport materials over long distances, these systems are built to handle high capacities and are ideal for surface mining and quarry operations. They offer efficient and cost-effective material transport solutions.
- Underground Conveyor Systems: These systems are specifically designed for underground mining operations. They are built to navigate tight spaces and handle the unique challenges of underground environments.
- Radial Stacker Conveyors: Radial stackers create large stockpiles of bulk materials. These conveyors can rotate and extend to distribute materials evenly, maximizing storage space and improving efficiency.
- Portable and Mobile Conveyors: Custom Conveyor Solutions offers a range of portable and mobile conveyors that provide flexible material handling solutions. These conveyors are ideal for temporary operations or sites where mobility is crucial.
- Stackers:
- Fixed Stackers: These permanent installations stack materials at a single location. They are designed for high-volume operations and provide reliable performance.
- Telescopic Stackers: Telescopic stackers offer extendable and retractable conveyor sections, allowing for flexible stacking at varying distances. They are ideal for operations that require dynamic material handling solutions.
- Gearboxes and Reducers:
- High-Performance Gearboxes: Custom Conveyor Solutions provides gearboxes engineered to deliver reliable power transmission and handle the demands of heavy-duty conveyor systems. These gearboxes are built to withstand high torque and provide smooth operation.
- Speed Reducers: Speed reducers are essential for controlling the speed and torque of conveyor belts. The company offers a range of reducers designed to meet the specific needs of different conveyor applications.
- Additional Conveyor Components:
- Idlers and Rollers: High-quality ones reduce friction and support the conveyor belt, ensuring smooth and efficient operation. They are available in various configurations to suit different applications.
- Pulleys and Drums: Pulleys and drums are critical components that drive and support the conveyor belt. Custom Conveyor Solutions offers a range of pulleys and drums designed for durability and reliable performance.
- Belt Cleaners and Scrapers: These components help maintain the cleanliness of the conveyor belt by removing material buildup and debris. This reduces wear and tear on the belt and improves overall efficiency.
Applications in Various Industries
Industries Served by Custom Conveyor Solutions
- Mining:
- Surface Mining: Custom Conveyor Solutions provides robust and reliable conveyor systems designed to handle the high-volume demands of surface mining operations. These systems efficiently transport raw materials such as coal, iron ore, and other minerals from the extraction site to processing facilities.
- Aggregate and Quarrying: Custom conveyor systems are crucial in aggregate and quarrying operations for moving crushed stone, gravel, sand, and other aggregate materials. These systems ensure continuous and efficient material flow from the quarry face to processing plants.
- Manufacturing:
- Food and Beverage Processing: Conveyors transport ingredients, finished products, and packaging materials in the food and beverage industry. The systems are designed to meet strict hygiene standards and ensure the safe handling of food products.
- Pharmaceuticals: Pharmaceutical conveyor systems transport raw materials, intermediate products, and finished drugs. They are designed to meet stringent regulatory requirements and ensure contamination-free handling.
- Logistics and Distribution:
- Warehousing: Custom Conveyor Solutions provides conveyor systems for warehousing and distribution centers, optimizing the movement of goods from receiving docks to storage areas and shipping zones. These systems enhance efficiency and accuracy in order fulfillment.
- E-commerce: The rapid growth of e-commerce has increased the demand for efficient material handling solutions. Custom conveyor systems facilitate product sorting, packing, and shipping in e-commerce fulfillment centers.
- Agriculture:
- Grain Handling: Conveyor systems are essential in agricultural operations for efficiently handling and transporting grains, seeds, and other bulk materials. These systems help streamline agricultural product storage, processing, and distribution.
- Livestock Feed: Conveyors transport ingredients and finished feed products in feed mills, ensuring efficient production and delivery to livestock operations.
- Recycling and Waste Management:
- Material Recovery Facilities (MRFs): Custom Conveyor Solutions provides systems for sorting and processing recyclable materials in MRFs. These conveyors help separate different types of materials for recycling, reducing waste, and promoting sustainability.
- Waste-to-Energy Plants: Conveyor systems transport waste materials to incinerators or other processing units in waste-to-energy plants, which convert waste into usable energy.
- Cement and Building Materials:
- Cement Production: Conveyor systems are crucial for transporting raw materials like limestone, gypsum, and clinker. These systems ensure efficient material handling from quarry extraction to final cement production.
- Construction Materials: Custom conveyors transport materials such as sand, gravel, and concrete, facilitating efficient construction processes.
Specific Applications in Mining and Other Sectors
- Mining:
- Ore Transport: Custom Conveyor Solutions designs systems for transporting ores from mining sites to processing plants. These conveyors handle heavy loads and are built to withstand the abrasive nature of mined materials.
- Overburden Removal: Conveyor systems transport overburden materials (the soil and rock layer above the mineral deposit) to waste dumps or designated storage areas. This efficient removal process helps to access the mineral deposits more effectively.
- Material Sorting and Processing: Custom conveyors are integrated into sorting and processing facilities to separate valuable minerals from waste rock. These systems enhance the efficiency of ore processing operations.
- Food and Beverage Processing:
- Ingredient Handling: Conveyors transport raw ingredients such as grains, sugar, and spices to mixing and processing units. These systems ensure a consistent supply of ingredients, maintaining production efficiency.
- Packaging and Distribution: Food and beverage products are transported via conveyors to packaging stations after processing. These systems streamline the packaging process, ensuring that products are quickly and accurately prepared for distribution.
- Pharmaceuticals:
- Cleanroom Conveyors: Custom Conveyor Solutions provides cleanroom conveyor systems that operate in controlled environments. These conveyors transport pharmaceutical products without risking contamination.
- Automated Sorting and Packaging: Conveyor systems automate the sorting and packaging of pharmaceutical products, increasing efficiency and reducing the risk of human error.
- Logistics and Distribution:
- Automated Sorting Systems: In distribution centers, automated conveyor systems sort packages based on size, weight, and destination. These systems increase the speed and accuracy of order fulfillment.
- Cross-Docking: Conveyor systems facilitate cross-docking operations, where incoming goods are immediately transferred to outbound transportation without long-term storage. This process reduces handling time and improves distribution efficiency.
- Recycling and Waste Management:
- Sorting Lines: Custom Conveyor Solutions designs sorting lines for recycling facilities, where conveyors transport mixed waste materials through various sorting stages. These systems help separate recyclable materials such as metals, plastics, and paper.
- Composting Operations: Conveyor systems are used in composting facilities to transport organic waste through different stages of composting, ensuring efficient processing and production.
- Cement and Building Materials:
- Aggregate Handling: Custom conveyors transport aggregates like sand, gravel, and crushed stone from quarries to processing plants. These systems ensure a continuous supply of materials for cement production and construction projects.
- Finished Product Transport: Conveyor systems move finished cement and other building materials to storage silos or loading areas, facilitating efficient distribution to construction sites.
Recent News and Updates
Industry Insights and Updates on Conveyor Belt Technology
- Technological Advancements:
- Smart Conveyor Systems: Recent advancements in conveyor belt technology have introduced smart systems incorporating sensors and IoT (Internet of Things) devices. These smart-systems enable real-time monitoring of belt performance, tracking wear and tear, and predicting maintenance needs. This technology helps minimize downtime and optimize maintenance schedules, leading to improved efficiency and cost savings.
- AI and Machine Learning: Integrating artificial intelligence (AI) and machine learning algorithms in conveyor systems has enhanced the ability to analyze operational data. These technologies can predict potential failures, optimize belt speeds, and adjust operational parameters dynamically, ensuring optimal performance and reducing the risk of unexpected breakdowns.
- Lightweight and Durable Materials: Innovations in material science have led to the development of lighter and more durable conveyor belts. High-performance fibers, such as Kevlar® and carbon fiber composites, offer superior strength-to-weight ratios, improving efficiency and reducing energy consumption. Additionally, polymer advancements have produced belts with enhanced resistance to abrasion, chemicals, and extreme temperatures.
- Energy-Efficient Motors: Adopting energy-efficient motors and variable frequency drives (VFDs) in conveyor systems has significantly reduced energy consumption. These motors adjust the speed and torque of the conveyor belt based on real-time load conditions, ensuring optimal energy use and lowering operational costs.
- Sustainability and Environmental Impact:
- Eco-Friendly Materials: The conveyor belt industry increasingly focuses on sustainability by developing eco-friendly materials. Biodegradable polymers and recyclable composites are being used to reduce the environmental footprint of conveyor systems. These materials not only enhance sustainability but also comply with stringent environmental regulations.
- Reduced Emissions: Implementing energy-efficient technologies and lightweight materials in conveyor systems contributes to lower greenhouse gas emissions. By reducing energy consumption and improving operational efficiency, these advancements help mining and manufacturing companies meet their sustainability goals.
Safety Features and Cost-Saving Strategies
- Enhanced Safety Features:
- Fire-Resistant Belts: Recent updates in conveyor belt technology include the development of fire-resistant belts. These belts are designed to withstand high temperatures and resist ignition, significantly reducing fire risk in hazardous environments such as underground mines and chemical processing plants.
- Anti-Static Properties: Conveyor belts with anti-static properties prevent the buildup of static electricity, which can pose a significant risk in environments with flammable materials. These belts reduce the potential for sparks and explosions, enhancing overall safety.
- Emergency Stop Mechanisms: Modern conveyor systems have advanced emergency stop mechanisms. These systems include strategically placed stop buttons and pull cords that allow workers to halt the conveyor immediately in case of an emergency, preventing accidents and injuries.
- Safety Guarding and Barriers: The latest conveyor systems incorporate comprehensive safety guarding and barriers to protect workers from moving parts. These features prevent accidental contact and reduce the risk of injuries, ensuring a safer working environment.
- Cost-Saving Strategies:
- Predictive Maintenance: Predictive maintenance technologies, such as condition monitoring sensors and AI-driven analytics, help identify potential issues before they lead to costly failures. By addressing maintenance needs proactively, companies can reduce unplanned downtime and extend the lifespan of their conveyor belts.
- Energy Management Systems: Implementing energy management systems that monitor and optimize energy usage can lead to significant cost savings. These systems adjust the operation of conveyor belts based on load requirements, reducing energy consumption during low-demand periods.
- Modular Design: The trend toward modular conveyor belt design allows for easily replacing individual components rather than entire systems. This modularity reduces maintenance costs and downtime, as damaged or worn parts can be quickly swapped out without disrupting operations.
- Material Optimization: Advances in material technology have led to the development of belts that require less frequent replacement. Using high-durability materials reduces the frequency of belt changes, lowering overall maintenance costs and improving operational efficiency.
- Operational Efficiency:
- Automation and Control Systems: Integrating automation and advanced control systems in conveyor technology enhances operational efficiency. Automated systems can manage the speed, load distribution, and material flow, ensuring smooth and consistent operation. This reduces manual intervention and allows for more precise control over the conveyor process.
- Load Management Solutions: Innovative load management solutions help optimize the distribution of materials on the conveyor belt, preventing overloading and reducing wear and tear. These solutions ensure that the conveyor operates within its designed capacity, enhancing longevity and reducing maintenance needs.
- Regulatory Compliance:
- Compliance with Safety Standards: The latest conveyor belt technologies are designed to comply with international safety standards and regulations. This includes adherence to guidelines set by organizations such as OSHA, MSHA, and ISO, ensuring that conveyor systems meet the highest safety and performance criteria.
- Documentation and Training: Companies are increasingly providing comprehensive documentation and training programs to ensure that workers are knowledgeable about the latest safety features and maintenance practices. This emphasis on education and compliance helps maintain a safe and efficient working environment.