Types of warehouse management systems
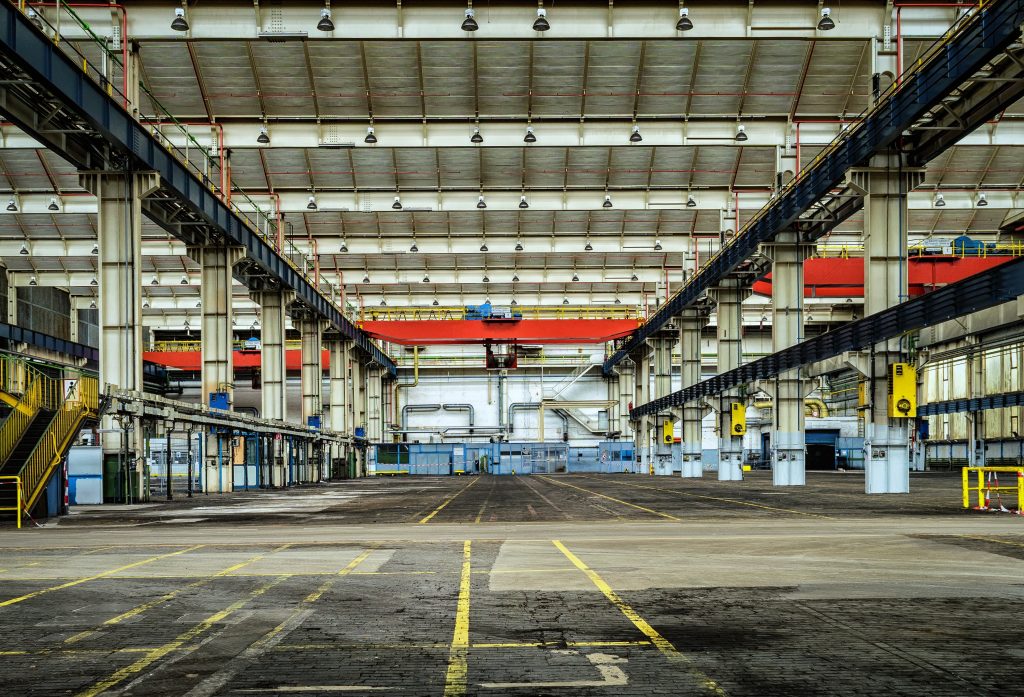
Optimizing warehouse operations in today’s fast-paced business environment has become a top priority for organizations. As technology advances, warehouse management systems (WMS) have evolved significantly, offering various functionalities and capabilities. Understanding the different types of WMS available is crucial for businesses looking to enhance efficiency, improve inventory accuracy, and streamline operations. This article explores the various types of WMS, shedding light on their unique features and benefits.
Type 1. Standalone as a warehouse management systems
A standalone warehouse management system (WMS) offers a range of benefits, particularly for smaller warehouse operations or businesses looking to enhance specific aspects of their supply chain without integrating a new system. While standalone systems may have limited features compared to comprehensive solutions, they remain cost-effective. They focus primarily on warehouse operations and inventory management, including warehouse inventory control.
Standalone systems are essential because they encompass the two core components crucial for warehouse functionality: warehouse operations and inventory management. They provide necessary functionalities without the complexities of broader supply chain management. For businesses seeking to improve specific facets of their supply chain, standalone WMS offers simplicity and quick implementation without waiting for full integration. This is especially advantageous for small warehouses still relying on manual processes and spreadsheets.
With a standalone WMS, businesses can efficiently manage critical warehouse tasks, including picking, packing, shipping, receiving, returns, FIFO or LIFO data management, cycle counts, barcode scanning, and inventory tracking. These features enable improved operational efficiency and accuracy, enhancing overall warehouse performance.
However, when choosing a standalone system, it’s important to consider the business’s scalability and future growth. While standalone systems may meet current needs, a more robust WMS should be considered if there are plans for substantial expansion and the adoption of more advanced technologies.
Type 2. ERP as a warehouse management systems
Enterprise resource planning (ERP) software falls under a comprehensive category of tools that empower companies to effectively manage and monitor their various operations and performance from a centralized location. By consolidating data into a single source of truth, ERP software enables businesses to gather and analyze information across different departments and sectors. This centralized approach facilitates efficient administration of all areas within the organization. Some of the reasons why supply chain management needs an ERP include:
- Improved visibility: ERP software provides real-time visibility into all aspects of the supply chain, which helps to identify bottlenecks and potential issues before they become major problems.
- Enhanced collaboration: ERP allows different departments and stakeholders to share data and collaborate more effectively.
- Increased efficiency: an ERP system automates many manual processes, reducing errors and increasing efficiency (for example, an ERP system can automatically generate and send purchase orders to suppliers based on inventory levels and production schedules).
- Better decision-making: An ERP system can, for instance, help identify the most cost-effective suppliers or the most efficient transportation routes.
Types of ERP systems
There are three basic categories of ERP systems, each with a selection of deployment models. The three most popular forms are on-premise, cloud-based, and hybrid.
- On-premise ERP software development is implemented onsite and maintained in actual office space within a business for complete management, support, and ownership of the entire system once established. It is hosted on the company’s computers and servers.
- Cloud-based ERP software is a web-based solution known as Software as a Service (SaaS). This is often accomplished through the payment of a subscription. An organization can access and save data on any device with an internet connection supported by the software vendor.
- Hybrid ERP software combines on-premises and cloud installation. Each provider offers a different hosting and deployment service combination. These models allow ERP users to switch between delivery paradigms or incorporate advantages not present in the current system.
Type 3. Cloud-based platform as a warehouse management systems
Opting for a cloud-based platform is the optimal solution for logistics management, facilitating swift integration and enhancing convenience. Utilizing cloud technology in warehouse management brings many benefits, including heightened security, reduced IT maintenance, and cost savings. Since cloud-based systems operate on external servers and infrastructure, the integration and management of the warehouse management system (WMS) become significantly simpler and more cost-effective. This eliminates the need for extensive implementation efforts associated with on-premises systems, streamlining the process and minimizing expenses.
A cloud-based platform offers several critical features that enhance its appeal:
- User-friendly: Cloud-based WMS solutions are designed with user-friendliness, ensuring ease of navigation and accessibility for warehouse staff.
- Scalability: Cloud platforms provide the flexibility to scale operations up or down seamlessly as business needs evolve, accommodating growth and expansion without disrupting workflows.
- Enhanced Security: Cloud-based WMS systems prioritize robust security measures, protecting sensitive data from potential threats and ensuring data integrity.
- Flexibility: Cloud-based platforms offer flexibility in terms of accessibility, allowing users to manage warehouse operations remotely and collaborate across different locations or with external stakeholders.
- Data and Disaster Recovery: Cloud-based WMS solutions typically include reliable data backup and disaster recovery mechanisms, ensuring that critical information is protected and can be recovered in case of unforeseen events.
- Competitive Advantage: Leveraging cloud technology gives businesses a competitive edge by enabling rapid response to market changes, efficient order fulfillment, and streamlined operations.
- Consolidation: Cloud-based platforms serve as a centralized hub, consolidating data and operations from various departments and locations, promoting data consistency, and improving overall efficiency.
Third-party logistics providers (3PLs) often opt for cloud-based platforms as they frequently outsource a significant portion of their warehouse operations. The cloud enables them to seamlessly integrate and manage all aspects of their business in a user-friendly format. If you are a 3PL Warehouse Manager, exploring cloud-based WMS solutions tailored to your needs is highly recommended.
Type 4. Supply chain as a warehouse management systems
In a rapidly changing business environment, the timely implementation of new methods, such as supply chain management (SCM), saves money and helps companies stay ahead of the curve.
Custom-developed online and mobile apps for logistics management automation are particularly relevant and beneficial for three primary business sectors:
- Sales: Implementing software in the supply chain opens up opportunities for more effective management and reduces the need for additional staff. Custom app development can help streamline processes and decrease reliance on website support teams.
- Control over storage inventory: Traditional business methods often require maintaining high inventory levels in warehouses. By employing automated market analysis through supply chain software, businesses can ensure that the quantity of items in warehouses aligns with projected sales. This helps optimize purchasing decisions, reduce costs, and avoid overstocking.
- Market research: Supply chain software facilitates market analysis and enables precise sales predictions. Through ongoing market research, businesses can anticipate future product trends and align their offerings accordingly. This helps them stay competitive and effectively meet customer demands.
Real-time product tracking technologies and solutions provide visibility throughout the supply chain. Manufacturers can track each unit in real-time, from production to the final consumer. This level of visibility allows for efficient scheduling, tracking, and monitoring of each product’s journey, ensuring smoother operations and improved customer satisfaction.
By leveraging custom-developed apps, real-time tracking, and market analysis, businesses can enhance their supply chain management processes, optimize inventory levels, improve sales forecasting, and adapt to changing market trends. This proactive approach enables companies to maintain a competitive edge and effectively navigate the dynamic business landscape.
What to know about the integration of warehouse management systems
Building such a software combination often seems daunting for businesses as it involves multiple processes and elements. Let’s outline the steps needed to develop a comprehensive logistics solution system.
Step 1: Analyze business needs and create an improvement plan.
Before implementing transport management software, it is vital to understand how your business operates and what the stakeholders’ expectations are. For example, logistics executives may expect higher ROI, smooth processes, and elimination of wasteful warehouse practices. Similarly, users may expect a simple system that alights with their workflow. Therefore, after assessing all risks and expectations, create a clear strategy.
Step 2: Gather an implementation team
To mitigate the risk associated with new system implementation, experienced installation teams are essential. Your team should select members with prior experience in dealing with a diverse range of logistics scenarios. The team should be cross-functional, with people from different departments, including IT, logistics, sales, etc.
Step 3: Partner with a management software development company
Logistics companies often fail to meet the implementation schedule. Reasons for failure include the absence of realistic plans, lack of technical expertise, and no prior experience with logistics software development. Hence, for WMS, TMS, and YMS implementation, it is essential to pick the right development team.
Step 4: Software testing and deployment
Once the software for the transport system is developed, it needs to be tested with actual logistics data and conditions. Various scenarios must be explored to assess system performance. All possible users and stakeholders must check for bugs and functional errors to ensure the software fulfills everyone’s requests.
Step 5: Train employees and take regular data backups
Staff must get familiar with the newly implemented solutions. Provide employees with the opportunity to learn, practice, and ask questions by undertaking various training sessions. It will boost staff productivity and, ultimately, the project success rate. Other than training, take data backups while shifting to a new system.
Step 6: Assess software performance for future improvements
As everything is running, it is time to evaluate transport system software implementation and performance. Conduct assessments on key performance metrics such as client satisfaction rate, return on investment, etc.